En exploration continue vers les voiles de demain
Incidence Technologies est unique en Europe
Créée en 2013, Incidence Technologies a pour vocation de fabriquer les membranes Incidence D4®, DFi® et de porter la Recherche et Développement (R&D) du groupe pour concevoir les voiles de demain.
Seul producteur en Europe de membranes filamentaires
Incidence Technologies possède sa propre ligne d’imprégnation pour fabriquer des « tapes » (rouleaux de filaments très léger et imprégné de résine) et ses propres robots de dépose.
Incidence Technologies maîtrise ainsi la totalité de la chaine de production depuis la fibre jusqu’à la membrane, ce qui permet une totale traçabilité des produits, un contrôle qualité précis, une meilleure réactivité et une totale adaptation des matériaux en fonction du programme du bateau.
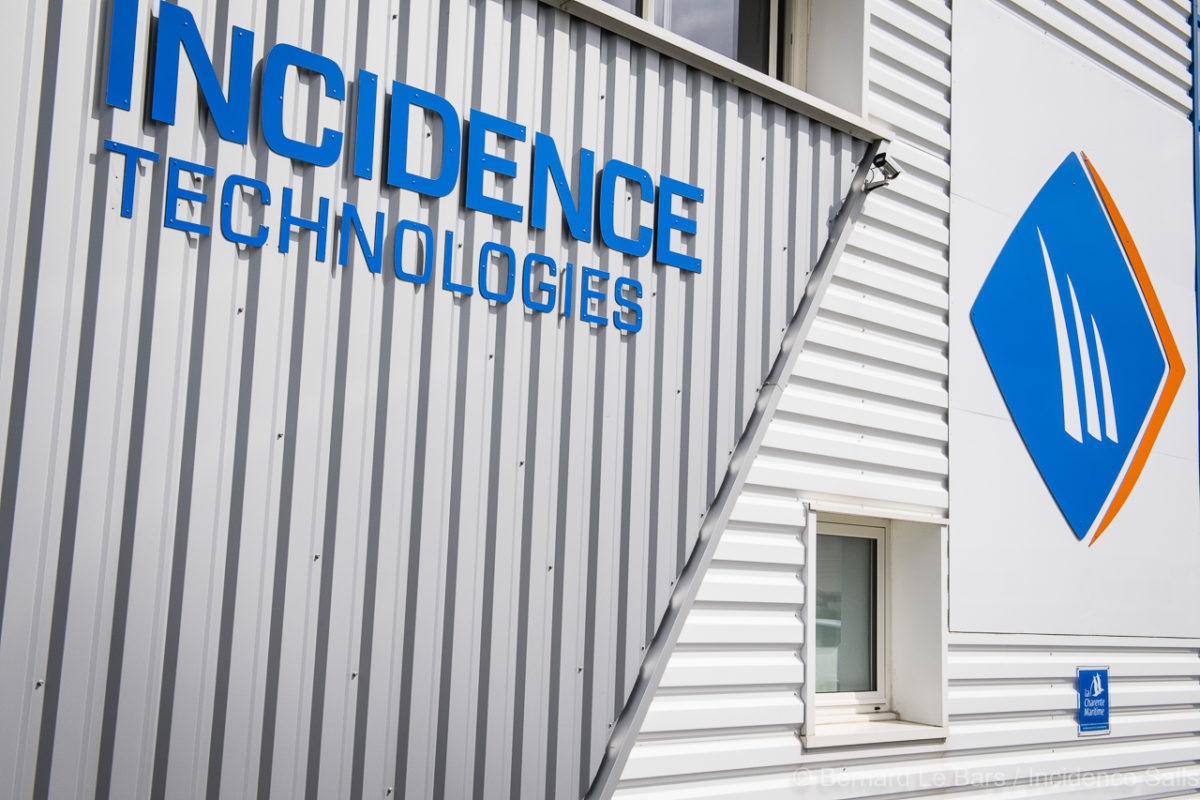
Centre de R&D
Incidence Technologies possède son propre laboratoire d’analyse afin de tester et mettre en œuvre les matériaux du futur, plus respectueux de l’environnement, plus performant et plus durables.
Cela permet de nombreuses collaborations technologiques avec d’autres secteurs comme le BTP, l’aéronautique ou le spatial.
Depuis 2015, deux brevets européens ont été déposés et Incidence a reçu le prix de l’innovation de la FIN en 2016.
L’innovation est au cœur de la stratégie d’Incidence.
Chiffres repères
Création en 2013
1er producteur de membrane filamentaire en France
2 300 m² de membrane produits par mois
1 bureau d’études et de recherches et développement sur les membranes
Capacité de calcul : code panneau et RANS (Reynolds Average Navier Stokes)
1 unité de production D4®, DFi®, DFi FIT®
Une membrane, qu’est-ce que c’est ?
Une membrane est un matériau composite structuré sur-mesure. La nature des fibres, leur quantité et leur direction sont ajustées de manière à répondre aux sollicitations mécaniques de la voile en navigation et correspondre au programme du bateau. Chaque membrane est unique.
Dans le D4®, ces fibres sont encapsulées entre deux films PET ou taffetas.
Dans le DFi®, il y a uniquement les fibres et de la résine, ce qui rend cette membrane plus légère, plus stable et plus durable.
Les calculs numériques d’Incidence Technologies,
des outils d’aide à la performance pour les coureurs
Incidence fait partie des rares voileries à proposer des études numériques FSI (Fluide Structure Interaction) poussées, via deux types de calculs : en code panneau et RANS (Reynolds Average Navier Stokes*). Des outils d’aide à la performance précieux pour les écuries de course au large.
L’équipe R&D d’Incidence Technologies et celle du BE d’Incidence Sails maîtrisent des outils de calculs numériques permettant non seulement de proposer des profils de voiles « performants et qui tombent pile comme il faut, dès les premiers essais », mais aussi de fournir de précieuses données aux écuries de course au large comme aux architectes navals.
Des aides majeures à la performance
Ces calculs numériques FSI ont pour objectif soit de calculer les différentes charges du gréement, soit d’optimiser des profils de voiles, soit d’obtenir la matrice aérodynamique du bateau (carte 3D des forces exercées sur le bateau).
Ces travaux peuvent être réalisés en étroite collaboration avec les architectes navals. Et, selon le cahier des charges, le délai de réalisation ou le budget impartis à ces études, l’équipe d’ingénieurs d’Incidence Technologies utilisera soit les calculs numériques en code panneau soit en RANS.
La voile parfaite
Les ingénieurs et dessinateurs d’Incidence Sails sont en mesure de procéder à des calculs avec des itérations RANS. Cette méthode permet de prendre en compte la fluidité et les turbulences des flux d’airs sur l’intrado et l’extrado des voiles.
A l’issue de ce processus assez complexe (cf. détails ci-dessous), le profil dessiné est parfaitement optimisé et en adéquation avec le cahier des charges initial : un gain de temps majeur pour les écuries de course au large.
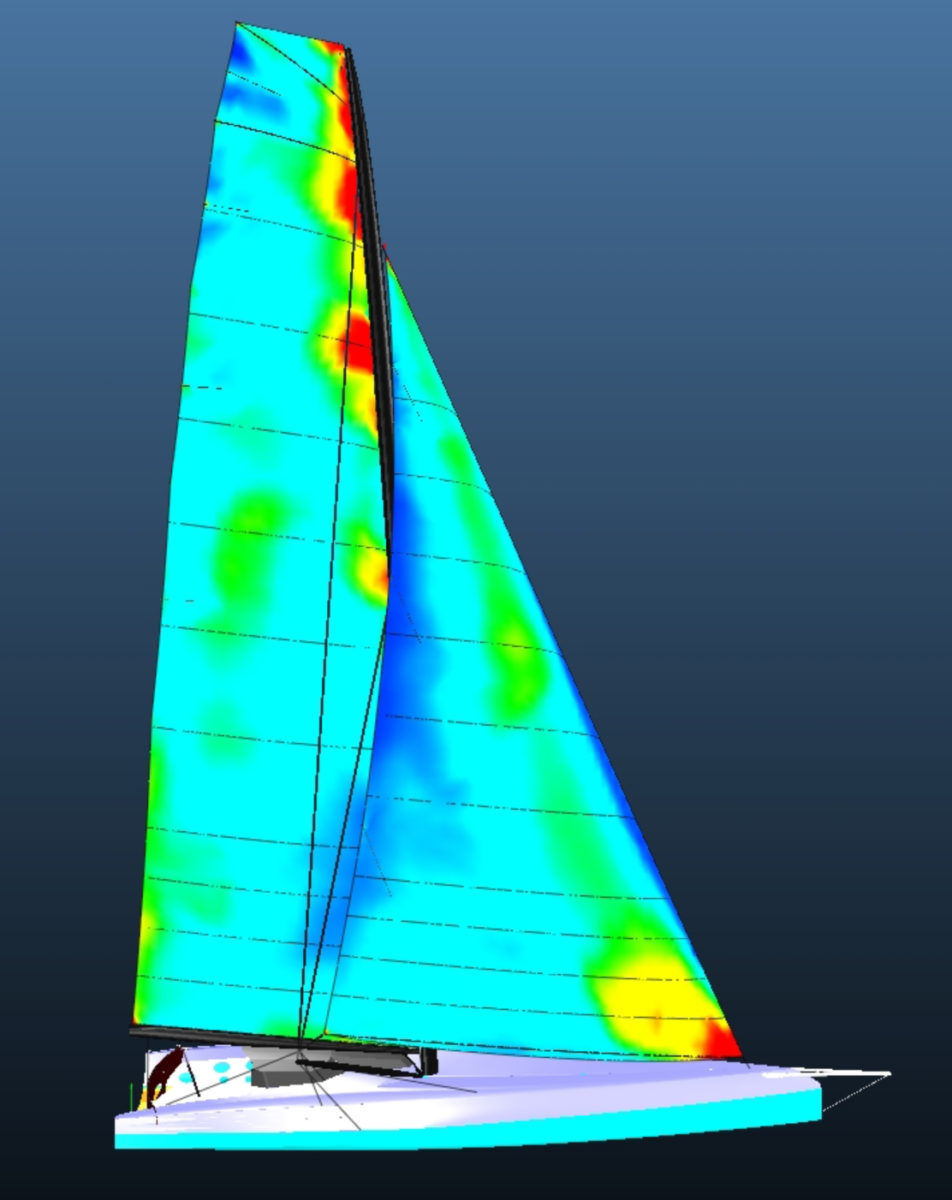
« Les profils tombent pile comme il faut. Il n’y a rien à redire. Il n’y a eu aucun aller-retour au plancher. C’est un gain de temps énorme pour nous », Sébastien Simon, skipper de l’IMOCA Arkéa – Paprec, équipé à 100% en Incidence.
« Je suis très content de mon jeu de voiles, je n’ai eu aucun retour au plancher à faire », Fabien Delahaye, skipper du Figaro Loubsol, équipé à 100% en Incidence.
Déterminer la trajectoire la plus rapide…
Les données hydrodynamiques des architectes navals et les calculs aérodynamiques réalisés chez Incidence Technologies permettent l’affinage de polaires et la création de VPP (Velocty Prediction Program). Ces VPP représentent l’ensemble des polaires virtuelles du bateau selon toutes les configurations de voiles et de réglages possibles du gréement, des foils…
Avec un VPP complet, associé aux statistiques de routages sur un parcours donné, il est possible de déterminer la trajectoire la plus rapide et les combinaisons de voiles les plus performantes pour ce tracé.
Pour résumer, qu’il s’agisse d’un simple calcul de charge ou de l’élaboration d’une matrice aérodynamique pour un VPP, l’équipe d’Incidence Technologies est en mesure de fournir aux écuries de course au large et aux architectes navals toutes les données nécessaires à leur recherche de performance.
* Navier-Stokes
En mécanique des fluides, les équations de Navier-Stokes sont des équations aux dérivées partielles non linéaires qui décrivent le mouvement des fluides newtoniens (gaz, liquides). La résolution de ces équations modélisant un fluide comme un milieu continu permet de proposer une modélisation de nombreux phénomènes : courants océaniques, mouvements de masses d’air, de liquides, comportement des gratte-ciel, de ponts…
Le nom de ces équations fait référence aux travaux de deux scientifiques du XIXe siècle : le mathématicien et ingénieur des Ponts Henri Navier, premier à introduire la notion de viscosité dans les équations d’Euler en 1823, et le physicien George Gabriel Stokes, qui a donné sa forme définitive à l’équation de conservation de la quantité de mouvement en 1845.
Détail des différents types de calculs réalisés par l’équipe d’Incidence
Calcul de structure/charge
Le calcul de structure permet de dimensionner les éléments d’accastillage du bateau. Les données de base sont en général les charges maximales applicables au gréement et aux voiles. Les calculs sont effectués en code panneau.
Optimisation de Flying Shapes
Afin d’optimiser un profil de voile, les dessinateurs d’Incidence vont chercher les forces maximales de poussée applicables sur la voile, tout en maintenant constant voire en réduisant le « heeling moment » (moment d’inclinaison du bateau).
Optimisation de la structure des voiles
L’optimisation de la structure des voiles a pour objectif d’optimiser la quantité de matières et la direction des fibres en fonction des déformations de la voile en navigation. . Elle s’obtient en améliorant la répartition des fibres (D4) ou des bandes de fibres (DFi® ; DFi FIT®), sans pour autant alourdir la voile.
Matrice aérodynamique
. Matrice aérodynamique obtenue avec un code panneau
Le logiciel d’Incidence Technologies exploite le code panneau, méthode de calcul pour laquelle l’écoulement des flux est considéré comme étant « non visqueux », « irrotationnel » et incompressible (ce qui correspond aux conditions de navigation au près, lorsque l’écoulement des flux est « attaché » aux voiles).
Les données ainsi obtenues permettent d’établir une première approximation des modélisations de profils et des données aérodynamiques.
Lorsque l’angle du vent apparent (AWA) devient trop important (supérieur à 35°), le code panneau ne permet plus d’obtenir des résultats précis, puisqu’il ne prend pas en compte le décrochage du fluide (flux d’airs) sur la voile. Il est alors plus pertinent de poursuive le calcul avec des itérations RANS.
. Matrice aérodynamique obtenue avec une itération RANS
« La méthode RANS consiste en la modélisation du mouvement d’un fluide newtonien en prenant en compte la fluctuation de la turbulence. Cette méthode permet d’obtenir des données précises quelque soit l’angle du vent apparent », explique Pierre-Antoine Morvan, responsable développement d’Incidence Technologies.
Dans son modèle RANS, Incidence peut prendre en compte les éléments aérodynamiques de la coque et du pont, afin de les prendre en compte dans le dessin de ses voiles.
Innovation 2020
Le Strong Luff : gain de vitesse et de polyvalence
Technologie sans câble novatrice
Le Strong Luff, mis au point par les équipes R&D d’Incidence Group et conçu par les mains expertes du plancher d’Incidence Sails, est une technologie de voiles d’avant en DFi® sans câble, novatrice.
L’atout majeur du Strong Luff est, comme son nom l’indique, la tenue du guindant.Cette tenue vient de la structure même de la voile en membrane filamentaire : les filaments de la membrane sont en effet placés en continu sur toute la longueur du guindant, du point d’amure au point de drisse.
Ce renforcement du guindant par des filaments en continu (en lieu et place du câble anti-torsion) permet :
- d’augmenter le range d’utilisation et les performances de la voile, grâce à une plus grande facilité de réglages et à un devers du guindant réduit.
- d’alléger la voile.
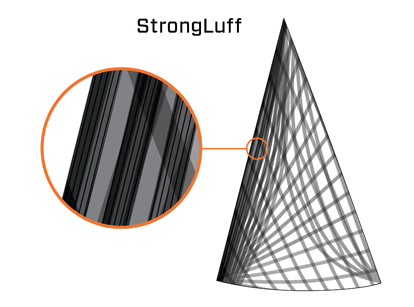
Une première !
Incidence est la première voilerie à avoir mis en place cette technique de dépose de filaments pré-imprégnées en continu sur plus de 30 mètres de long. Cette innovation est possible grâce au format et aux équipements du plancher d’Incidence Technologies.
La continuité des filaments entre l’amure et la drisse distingue le Strong Luff de la majorité des autres systèmes d’enroulement sans câble.
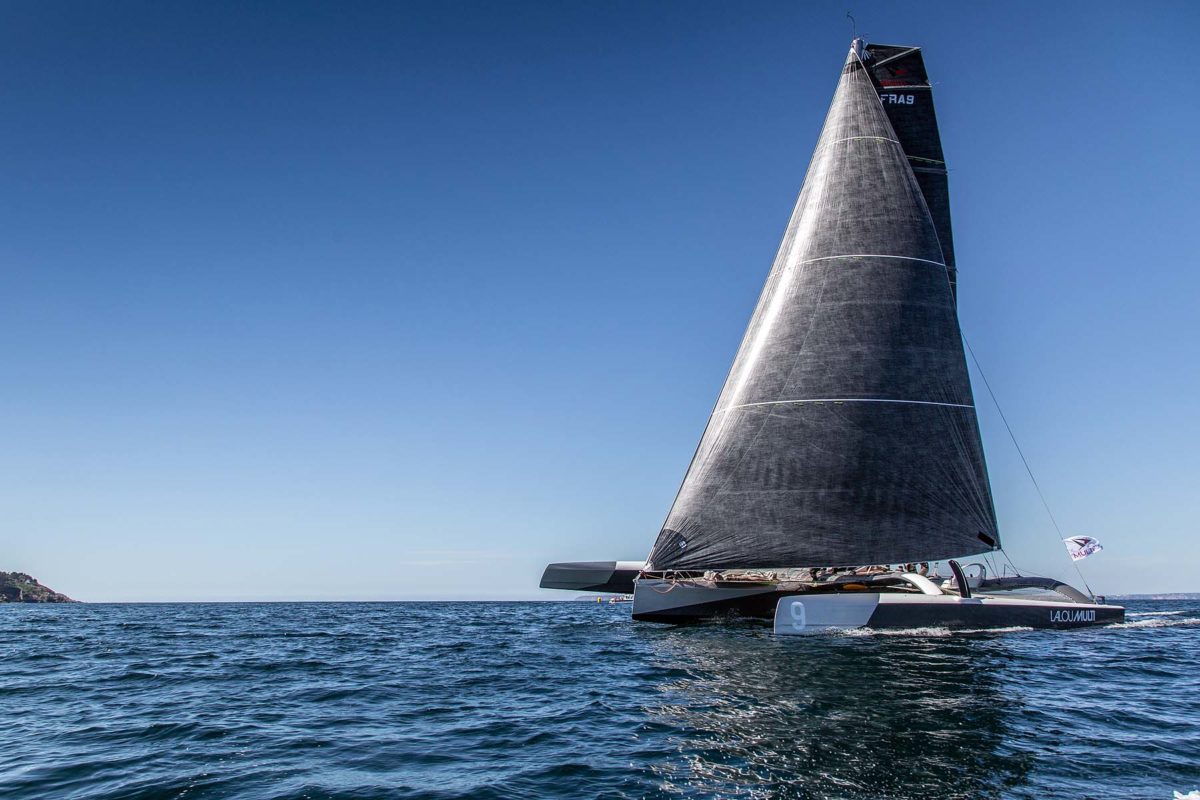
Lalou Roucayrol
« J’ai toujours été en confiance avec la voilerie Incidence et satisfait des innovations proposées. Ca a toujours apporté un gain de performance. Nous n’avons donc pas hésité pour essayer ce gennaker Strong Luff.
Le gennaker 2018 était vraiment très beau, cette voile-ci s’appréhende différemment. Il a fallu apprendre à la régler, car on peut travailler aussi sur le guindant : le gain est énorme.
Au cours des trois Grand Prix (Grand Prix Valdys à Douarnenez, Trophée des Multicoques Baie de Saint-Brieuc à Saint-Quay-Portrieux, Grand Prix Brest Multi50) on a pu le tester dans toutes les conditions de mer et de vent : on a gagné en performance et en polyvalence partout !
Les réglages sont beaucoup plus sensibles et dynamiques grâce au Strong Luff, associé à la raideur du DFi®. Cela permet des accélérations beaucoup plus rapides encore qu’avant.
Nous avions les plus belles voiles de la flotte ! »
Quentin Vlamynk
« Il nous fallait un nouveau gennaker, polyvalent, qui tienne pour les deux saisons à venir. Incidence nous a proposé de tester leur nouvelle version sans câble. C’est vraiment un gros plus : la voile se roule beaucoup plus vite, le bord d’attaque est plus fin. La voile est plus plate, le creux plus homogène. Elle se règle différemment : on joue sur le guindant et la bordure… le gain de vitesse est impressionnant.
On n’a plus du tout de plis horizontaux sur le guindant puisque c’est directement pris dans les fibres. Le DFi® et le DFi FIT®, sont toujours aussi efficaces. A chaque nouveau jeu de voile, ça s’améliore ! »
Les secrets de fabrication des membranes Incidence
La membrane filamentaire fabriquée par Incidence Technologies, est conçue en interne, en France.
Laminage à 7 bars de pression
Ces membranes sont pressées à chaud, à environ 7 bars de pression. Des tests effectués chez Incidence Technologies ont montré qu’une membrane laminée à 7 bars est 30% plus fine et 23% plus résistante à la déchirure* qu’une membrane laminée simplement sous vie (avec 1 bar de pression).
* Ce test de déchirure consiste à évaluer l’adhésion entre les fibres et la résine, donc la qualité de lamination.
Tableau des fibres
Performance |
Durabilité |
||||||
Ténacité | Module | Tenue de forme | Bilan | Résistance Flexion* | Résistance UV** | Bilan | |
cN/dTex | cN/dTex | commentaire | note/10 | perte % | mois | note/10 | |
Aramide | 21,4 | 813 | correcte | 9 | 25 | 2 | 7 |
Dyneema | 35,1 | 1160 | moyen | 6 | 0 | 7 | 10 |
FIT | 29 | 1050 | excellent | 9,5 | 2 | 1 | 9 |
Vectran | 28 | 654 | excellent | 8 | 2 | 1 | 9 |
Carbone | 33 | 1578 | excellent | 10 | 100 | infini | 1 |
PEN | 8 | 187 | correcte | 3 | 0 | 6 | 9 |
Polyester | 10 | 77 | correcte | 2 | 0 | 6 | 9 |
Nylon | 9,5 | 45 | correcte | 1 | 0 | 3 | 5 |